Reading time: 2 minutes
Automation as the key to increasing efficiency
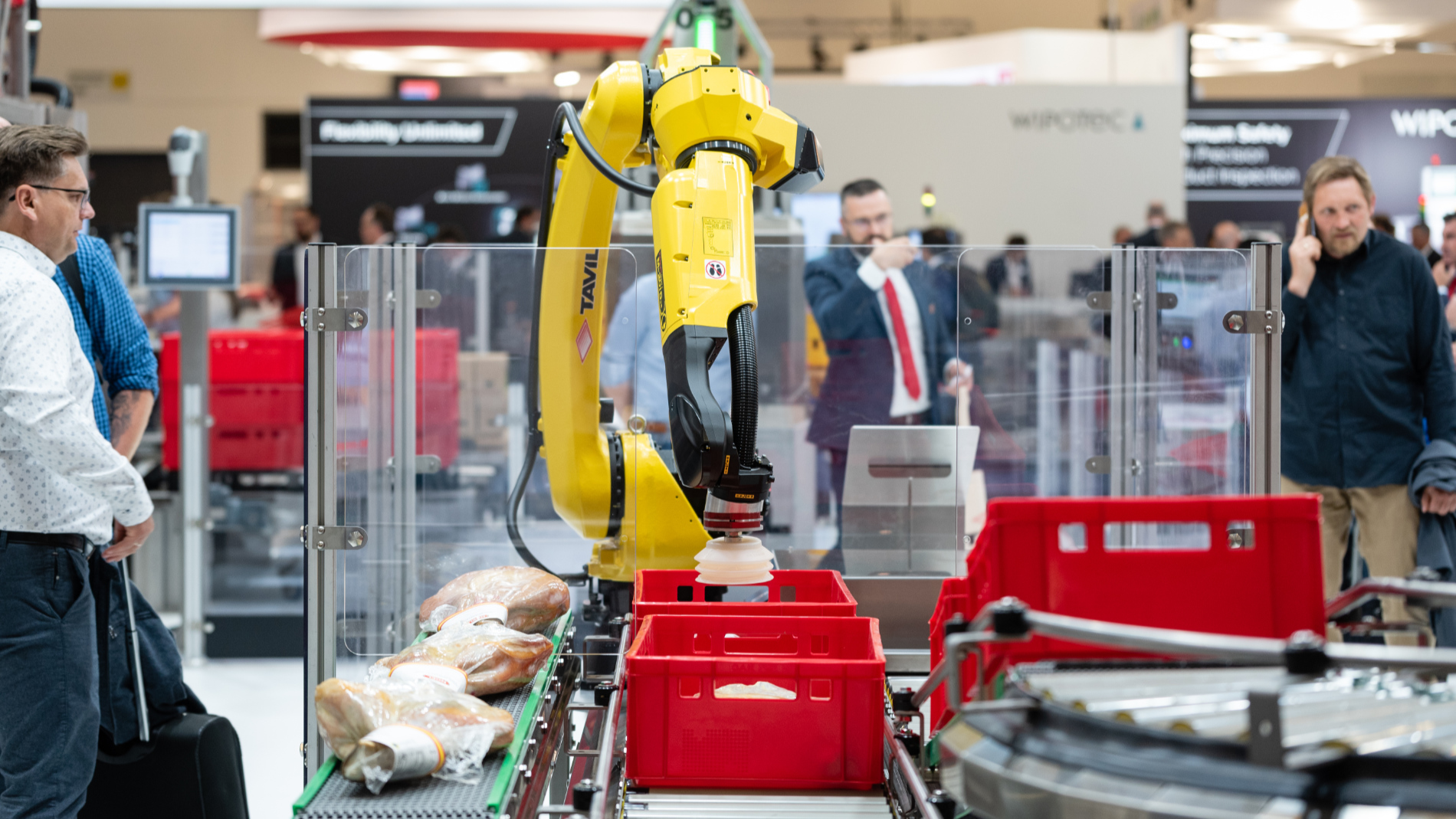
Automation plays a crucial role in numerous industries and has long been indispensable in food processing too. It not only optimises the operation of machines and systems, but also helps to reduce production downtime, save energy and materials and ensure compliance with legal requirements. Especially in the quality control and traceability of food, automation helps to ensure consistently high standards. It also offers a solution to challenges such as rising costs and a shortage of skilled labour.
In meat and protein processing, automation covers all production steps - from raw material preparation and processing to packaging and logistics. However, there are still gaps in the networking of individual production lines in many companies, which means that valuable data cannot be optimally utilised. This is where modern, web-based process control systems such as MES (Manufacturing Execution System) and ERP (Enterprise Resource Planning System) can help. As they are modular in design, they can also be integrated into existing plants - the benefits of a connected smart factory are therefore not just reserved for new production plants.
Real-time data for optimised production
Many automated processes are based on recording and analysing real-time data. Modern sensors record precise values for temperature, humidity, weight or pressure. For example, temperature and humidity sensors in cold stores prevent potential contamination by recognising temperature increases at an early stage. Weight sensors ensure that products meet the packaging specifications, minimising material waste and returns. Sensors are also used in the packaging itself, for example to keep the gas composition in modified atmospheres constant.
AI-supported processes for greater efficiency and safety
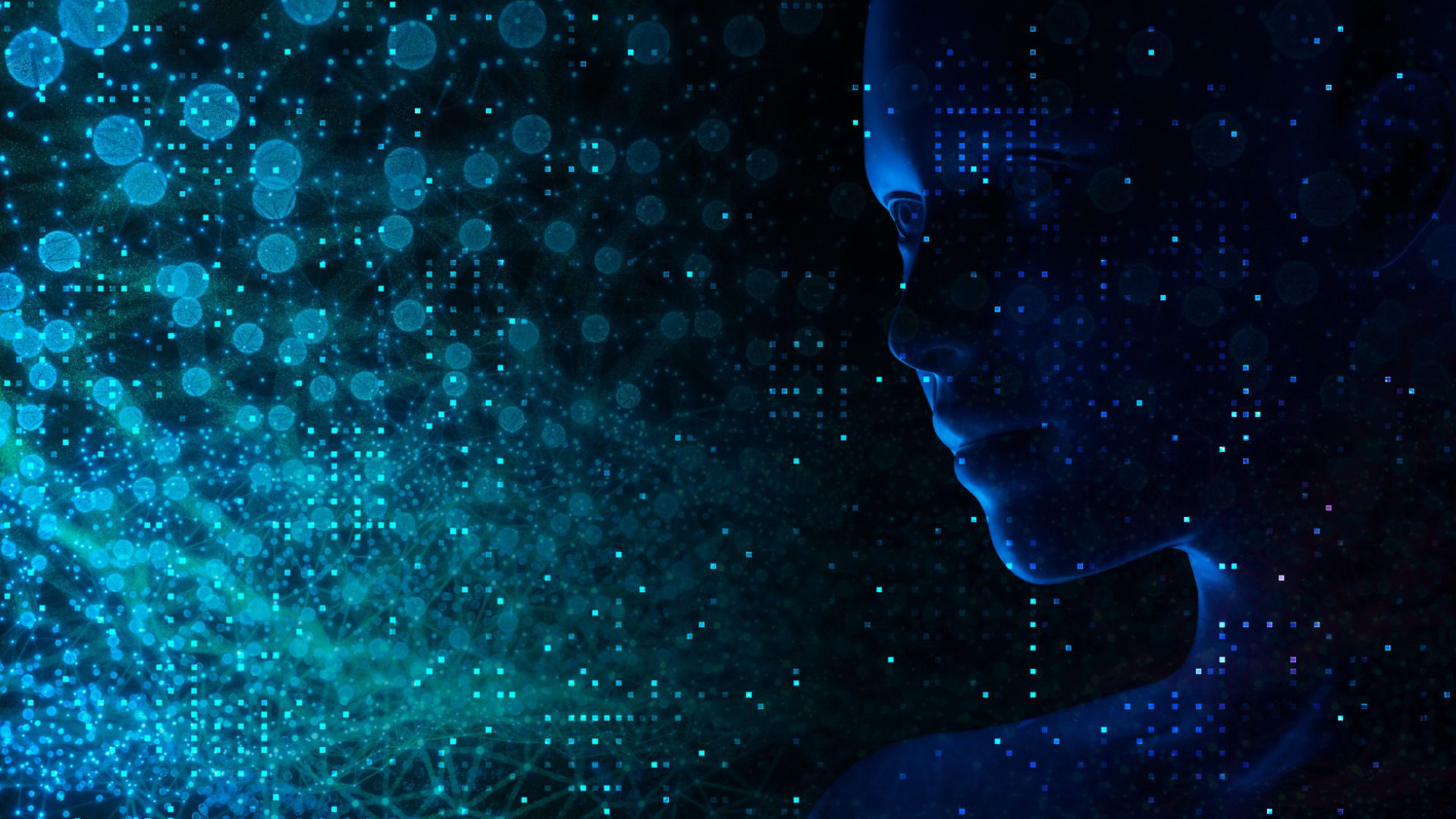
Artificial intelligence is fundamentally changing meat and protein processing. It enables machines not only to collect production data, but also to analyse it and derive patterns from it. This allows disruptions in the process to be recognised at an early stage and production errors to be corrected directly during operation. This not only increases efficiency, but also improves product safety.
A key area of application for AI is industrial image recognition. Specially trained models sort meat products according to size, shape and structure or evaluate quality characteristics such as grain or fat content, which can increase the sales value. AI is also used in quality control: Image processing systems inspect the entire production process in real time and identify colour deviations, foreign objects or packaging errors.
Another advantage is the use of AI for predictive maintenance. Intelligent systems monitor the condition of machines and predict potential failures so that maintenance measures are carried out exactly when they are needed. Studies show that predictive maintenance can reduce downtimes by up to 50 per cent and extend the service life of systems by up to 40 per cent.
Robotics at a new level thanks to machine learning
Industrial robots have long been standard in many large food companies. They perform monotonous tasks such as cutting, portioning, packaging or sorting and work around the clock with the utmost precision. The integration of AI is bringing further progress here: Thanks to machine learning, robots are increasingly able to adapt to new situations independently and act more flexibly.
One example of this is autonomous mobile robots (AMR), which use sensors and cameras to independently analyse their surroundings. They dynamically adapt their routes when obstacles appear and make independent decisions in unstructured production or logistics environments. In modern distribution centres, AI-supported industrial robots select the right goods, pick orders, sort out faulty products and recognise different packaging formats - with pick rates of up to 1,400 items per hour.
Robotics also increases efficiency in meat processing. Robots cut meat precisely at the desired angle and portion it exactly to the target weight. This minimises the loss of raw materials and increases production throughput. Multifunctional robot work cells, which are gradually replacing conventional production lines, are particularly forward-looking. They enable the parallel processing of different meat products within a flexible, autonomous network - a decisive advantage over rigid line production.
Technology as a driver of change
Meat and protein processing is at a turning point. AI, robotics and sensor technology are opening up new opportunities to make production processes more efficient, sustainable and economical. Companies that integrate these technologies at an early stage secure decisive competitive advantages and are ideally equipped for the future.
Discover relevant providers
Providers: Robotics
Providers: Artificial intelligence
Providers: Sensor technology
Providers: Automation